Recently, we have reached cooperation with Nigerian customers and successfully sold three 300kg/h chin chin production lines.
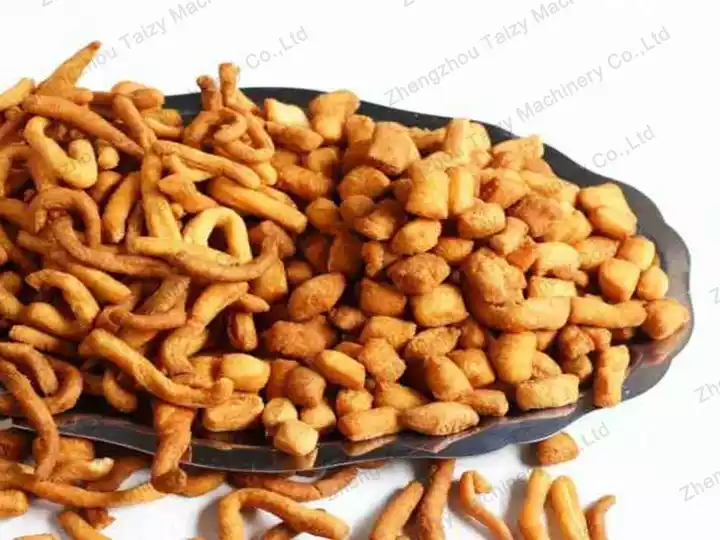
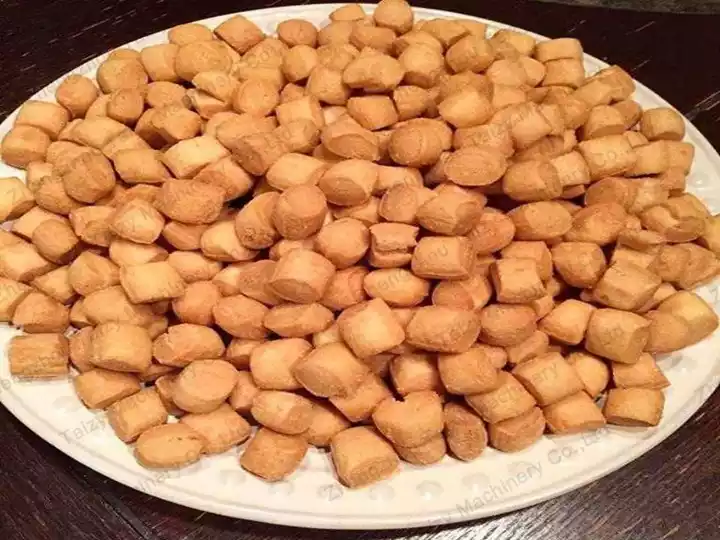
Challenges faced by Nigerian customers
With the continuous advancement of globalization, chin chin, as a popular traditional snack in Nigeria, is being loved by more international diners. Therefore, the market for chin chin is gradually expanding. Making chin chin by hand is inefficient and the product quality is inconsistent. Therefore, a Nigerian food processing factory urgently needed to expand its scale.
Customers are eagerly looking for machinery that can produce chin chin in large quantities. Discovered our food products and found us on the YouTube platform. Our sales manager learned about the customer’s situation and found that the customer had clear goals in purchasing the chin chin production line: to improve production efficiency, ensure product consistency, reduce long-term operating costs, and expand market share.
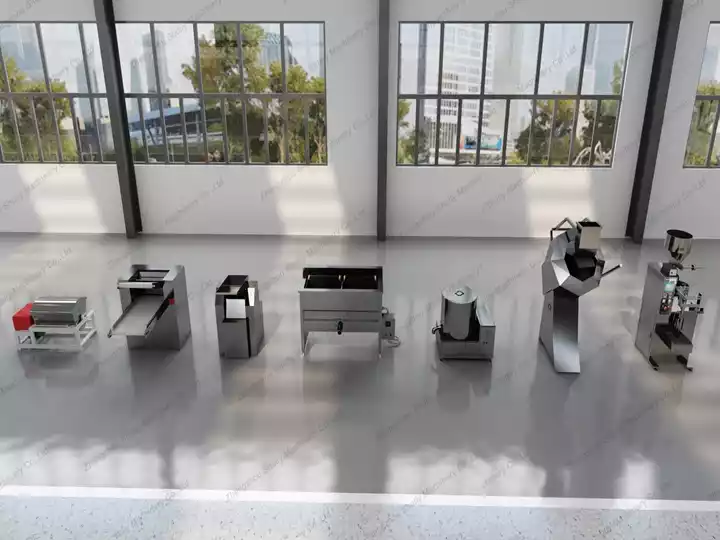
Characteristics of chin chin production line
In response to customer needs, we provide a complete chin chin production line, including dough mixers, dough presses, cutting machines, frying machines, oil removers, seasoning equipment, and packaging machines. This equipment has a high degree of automation and greatly improves production efficiency, ensuring consistent quality for each batch of Chin Chin.
Improved production efficiency: after installing the new chin chin production line, the Nigerian company’s production efficiency increased by more than 30%, product quality was more stable, and the scrap rate was significantly reduced.
- Save labor costs: with a high degree of automation, labor costs are also significantly reduced.
- Intelligent control: fully automated control system, one-button operation, reducing human errors.
- Customized design: customized according to the specific needs of the Nigerian market, such as the size, shape, and taste preferences of chin chin.
- Safety and hygiene: made of 304 stainless steel to ensure product hygiene and safety.
Teams work closely together
Solution design and customization
- Arrange online meeting: in-depth discussion of the customer’s current production bottlenecks, desired production capacity goals, product specification requirements, and budget range.
- Design production line plan: including equipment selection, the plan pays special attention to adapting to Nigeria’s power supply conditions, raw material characteristics, and local consumer preferences.
- Plan discussion and modification: multiple video conferences were held to discuss the design plan in detail. The customer put forward several modification suggestions, and we responded quickly and adjusted the plan.
Contract signing and production preparation
After clarifying all technical details and commercial terms, the two parties formally signed a cooperation agreement, including equipment list, price, delivery date, payment method, and after-sales service commitment.
- packed dough sheeter
- packed single machines
- shipped machines
- workers are packing machine
Installation and employee training
- Logistics arrangements: considering the logistics challenges in Nigeria, we have carefully arranged sea and land transportation to ensure that the equipment arrives at the customer’s factory safely and on time.
- On-site installation: an installation team composed of experienced engineers flew to Nigeria to be responsible for on-site assembly and debugging of the production line.
- Operational training: organize customer operators to conduct comprehensive training, covering equipment operation, daily maintenance, troubleshooting, etc.
Formal operation and customer positive reviews
The chin chin production line was successfully transferred to formal production, customer production capacity was greatly increased, and product consistency and market response exceeded expectations. Customers expressed high satisfaction with the cooperation and the positive impact of the production line on their business.